Disclaimer: We sometimes use affiliate links in our content. For more information, visit our Disclaimer Page.
It is more important in today’s competitive business world than ever to have an outstanding lean management plan. So if you want to take your business from good to great and ensure that your company is on the cutting edge of technology, then read this blog post for a few tips.
In this blog post, you will learn how to create an outstanding lean management plan for your business. This is a must-read if you want to improve customer service and make your company more competitive in the marketplace. The first step is understanding what lean management entails and how it can help your company succeed. Next, we’ll talk about the steps involved in creating an effective plan so that you can successfully implement these strategies at work!
What is Lean Management?

From the term alone, it seems like a system of management that must be lean. But what does “lean” mean in this context, and why would anyone want to use such a method for managing their business or team?
The answer lies with you – your company may have redundant processes (e.g., two people doing tasks separately one after another), waste products being created from these processes without adding any value, defects because those same individuals who were working redundantly take longer than necessary on each task because they don’t know how to do something differently, etc.).
If so, then perhaps Lean Methodology can help solve some of those problems by eliminating unnecessary steps out of the process, reducing inventory levels by decreasing lead times between.
Lean management methodologies are a way to maximize value from activities while reducing and eliminating waste in the process. Waste is eliminated by improving workflow, cutting back on redundancies, which can save you time, money, or energy.
When applied properly to your production process, lean generates huge improvements in efficiency, cycle time, productivity, material costs, and scrap.
The Lean concepts originated with Toyota’s production system, which was started more than 50 years ago when they were struggling financially after World War II. They used it first on their assembly line but eventually for all aspects of how they manufactured cars–everything from design through distribution so customers could get them quickly. At the same time, supplies lasted and did not have too much inventory sitting around waiting to be sold.
5 Key Lean Principles
Lean methodology has been proven to be one of the best ways for businesses to reduce waste and improve efficiency. By applying lean principles, organizations can cut costs by reducing non-value added activities from their process while improving productivity to better compete with other companies that are not using these methods. Lean methodologies have five key principles:
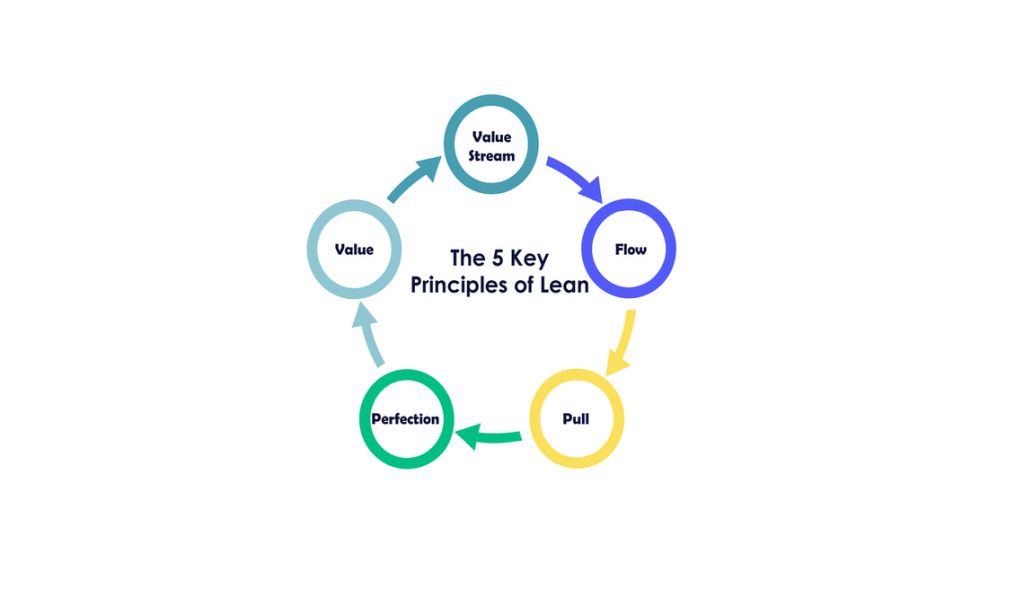
1. Value
Value is relative to the customer and their needs. Lean producers focus on what they will pay for, which depends on various factors like quality, delivery date, or price point depending on how much importance they place in these different aspects of value and fulfilling other requirements that customers may have such specific expectations.
2. Value Stream
Map of all the steps from raw materials to delivery used in making any product. The goal is to identify and eliminate each step that does not create value for your company or customer.
3. Flow
After removing waste, lean companies ensure the production process flows smoothly without interruptions. This may require cross-functional collaboration across all departments to eliminate bottlenecks and delays for a smooth flow of materials from start to finish.
4. Pull
Improved flow slashes time to market, so producers can deliver products as needed. “Just in time” manufacturing reduces the need to build or buy products in advance, saving money for manufacturers and their customers while also reducing waste from unused inventory that may go bad before it is sold anyway.
5. Perfection
Lean thinking and process improvement is a never-ending cycle. The more gains we realize, the greater our responsibility becomes to maintain them by using lean principles on an ongoing basis.
Lean management principles
Businesses have adopted lean management principles to reduce waste. Companies that utilize this style of management often define value from the standpoint of their end customer identify each step in a business process and eliminate those steps that do not create any additional value for them or their customers.
They also ensure they create maximum efficiency with every possible activity within these processes by eliminating redundancy wherever it is found. Making all necessary activities happen at such speed to ensure quality along the way without compromising on time-efficiency goals set out beforehand.
Why Lean is So Important in Managing a Business
The Lean methodology is a widely-adopted business strategy for manufacturing that focuses on customer value, cost reduction, and cycle time. This method aims to increase the output with less input by eliminating waste or anything else not needed to meet these goals.
This idea has been adopted from companies like Toyota Motor Corp, known worldwide as leaders in lean production techniques. By focusing more on what matters than any extraneous items, manufacturers will cut down costs while also providing higher quality goods at an affordable price point.
To remain competitive, companies must find ways of being more efficient. One way is by using lean management principles. If you’re a business owner and not sure what this means, then know that it’s all about reducing waste in your workplace so the company can turn out products with less expenditure of time spent on any given process. In other words: efficiency!
Lean management is vital to the success of any enterprise. It emphasizes lean manufacturing, which involves eliminating waste and streamlining processes to maximize efficiency with minimal cost. This approach stems from a belief that every aspect can be improved upon continuously over time if evaluated objectively for potential improvement opportunities or problems – sometimes referred to as ‘continuous process improvements. Lean includes techniques such as kaizen (a Japanese word meaning “improvement”), kanban systems (to improve production flow), 5S methodology, Heijunka principles (even levels of workloads), and much more!
Lean management benefits organizations by focusing on improving all parts of the work process throughout every company’s hierarchy. Specific processes that allow this include lean manufacturing and lean software development and other practices such as Lean Six Sigma, Lean Startup methodologies, or Value-based Healthcare Management.
Related Article: Create a Great Management Team for Your Business
Lean Management and Innovation
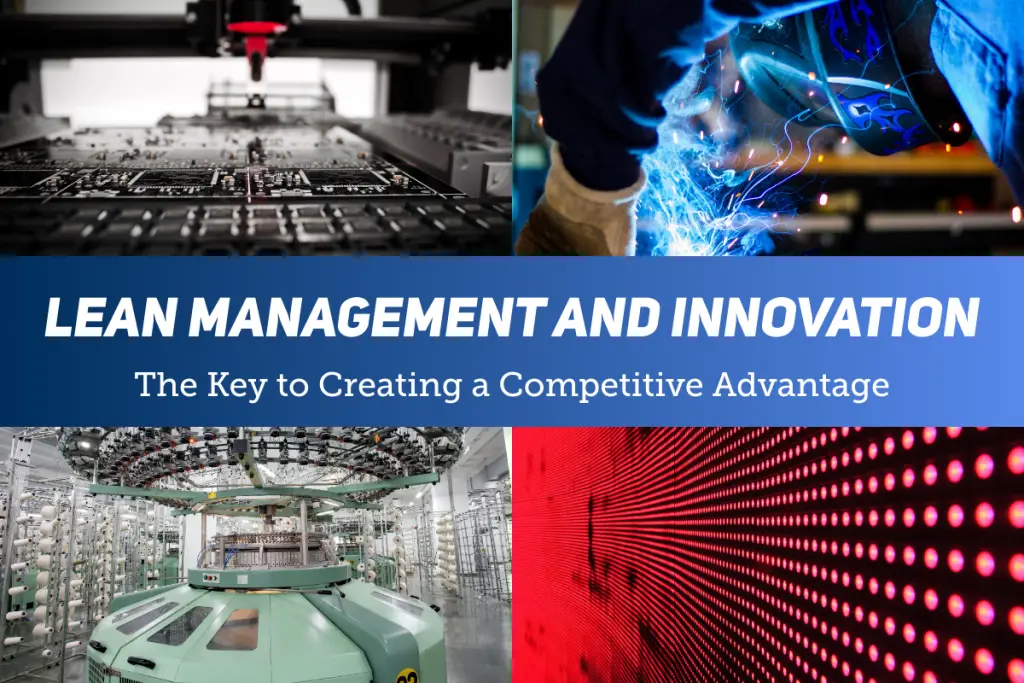
Innovation is key to success in the modern business world. One of the most effective ways for a company to innovate is by implementing lean management as it provides an organizational framework that promotes continual improvement and innovation, allowing individuals within organizations both large or small alike to eliminate waste while driving up quality levels at decreased time frames all while achieving greater efficiency inside their respective departments.
With these benefits available today more than ever before through this revolutionary way of thinking about management, companies will be able to fully leverage lean with its many additional advantages, including lower operating costs due exclusively from increased production volumes because every process has been optimized so that nothing gets wasted – in order words each different function becomes autonomous; higher employee morale due primarily from less stress among employees who are constantly encouraged.
Lean management makes good sense for innovation because it helps companies achieve the right balance of lean and agile manufacturing. Organizations can do this by implementing a system that minimizes waste, improves customer responsiveness, cultivates worker creativity, and fosters an environment where managers are free to experiment with different ways of doing things. This combination will streamline the process, produce higher-quality items at a lower cost, and speed up cycle times.
Innovating with lean management is a great way to reduce the risks of innovation and reap huge benefits from employees and customers alike. Lean firms can innovate without putting their finances at risk, making them more competitive in today’s fast-paced marketplace.
Related Article: How to Turn Your Idea into Reality
The Benefits of Lean Management
In the modern age, companies often focus on efficiency and predictability. Lean management is a strategy that can help you do both of these things in your company.
It’s often said that lean management is all about maximizing efficiency, and this may be true. But, it also goes above and beyond to create a culture of continuous improvement in the workplace, emphasizing teamwork. In addition, it takes into account every process from product design to customer service, which ultimately leads to increased profitability for your company!
The benefits of lean management are vast. It comes with several positive outcomes, including improved productivity, better customer service, and more efficient operation within your company. Lean also minimizes the amount wasted from spending that is not needed, such as excess inventory or unused packaging materials, which lowers costs while increasing profit margins.
The Risks of Lean Management
The process of lean management is a great way to help your company become successful. However, it also has some risks that are not often talked about. The biggest risk, in my opinion, is the fact that all employees may be willing to work hard for you at first. Still, once they see how much pressure they’re under and realize there’s no air or room left for creativity, many will start looking elsewhere (or worse), quit altogether.
The individual’s creativity is limited by the strict demands of a lean system. They may feel like they are constantly under surveillance, and starting up this type of process can be expensive in terms of production costs. In addition, the increased time spent on repetitive tasks and less personal interaction with the environment can lead to safety risks.
Nevertheless, when properly managed, these risks can be minimized by paying attention to how people react during the implementation stages of change (i.e., increased communication with workers).
How lean management is implemented dictates the company’s ability to succeed. It can help you maximize profits, but it doesn’t work if employees aren’t willing and able to take risks for this system–so be sure that your team has what they need before implementing anything.
5 Steps to Create a Solid Lean Management Plan
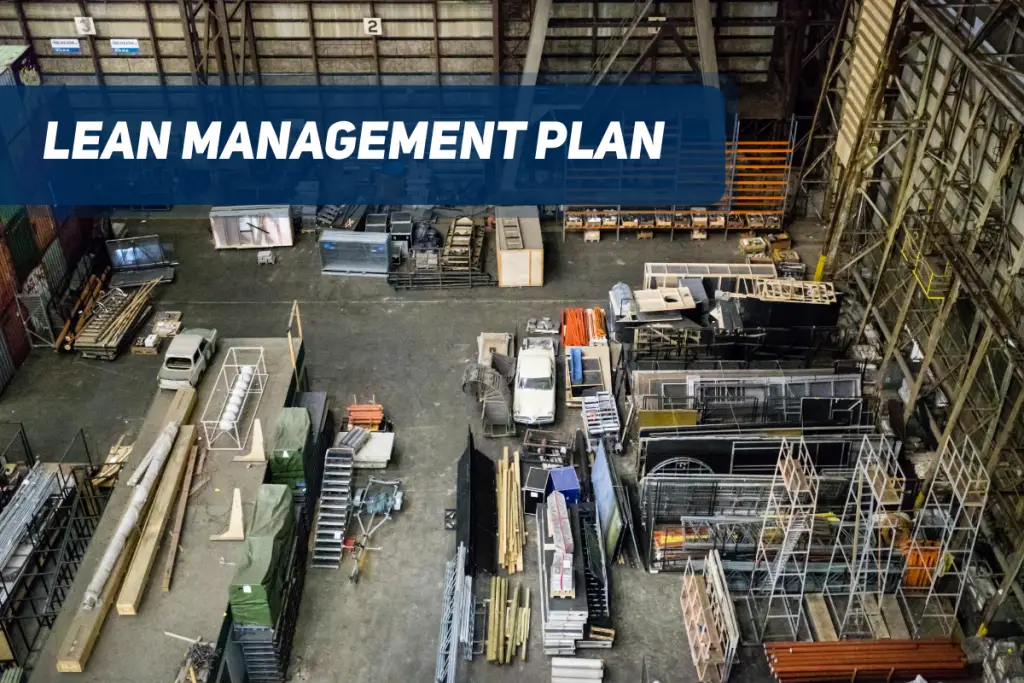
After analyzing your company’s needs, you will need to create a lean management plan. This 5-steps process is an easy way to approach it:
Step 1. Evaluate the needs of clients and find a way to add value for them to be satisfied.
Identify and create products or services that add value to a client´s objectives, ensuring full customer satisfaction. Identifying the business process or function that needs improvement is crucial: identify what is going well and identify areas of opportunity for potential improvements. What issues do you want to be tackled? For example, if production efficiency and quality control needed improving, an investment in both could prove worthwhile!
Step 2. Value stream mapping. This is a visual representation of the workflow in your company. It includes all actions and people involved with delivering the end product to customers, which allows you to identify what parts of this process provide no value.
Identify the vital steps that facilitate an efficient production or service line and unnecessary steps that waste resources. Then, optimize your workflow by eliminating wasteful processes to create a more streamlined value stream with better quality output.
Step 3. Eliminate steps in the workflow that may potentially cause interruption, backflow, delay, or destruction. Instead, create efficient and uninterrupted steps to form a value flow.
The company’s production process is a complex system of moving parts. Ensuring that each step flows smoothly without interruptions requires constant cross-functional collaboration, which can be difficult for departments to maintain. As such, it falls on the shoulders of employees with strong leadership skills and an eye for detail to make sure everything runs as efficiently as possible!
Step 4. Improved flow slashes time to market, so producers can deliver products as needed.
Supply only when needed, produce what’s demanded by the customers. When there is no demand for a product because it has not yet been ordered or manufactured, that means you’re wasting precious resources and time on something; who knows if they’ll ever use it again. But with “just-in-time” manufacturing practices such as Kanban cards (which are used to determine how many of each part should be made), manufacturers can precisely know just how much inventory they need, so businesses don’t have to overproduce anything–saving them money while also reducing waste.
Step 5. In the pursuit of perfection, lean thinking and process improvement is a never-ending cycle.
The more we accomplish with this mindset, the greater our responsibility becomes to maintain these gains by using lean principles on an ongoing basis. Strive for perfection through the continual removal of successive layers of waste as they are uncovered to get closer and closer to that goal every day!
How to Improve Your Lean Management Plan
It’s not enough to say that you’re going to be leaner. It would be best if you had a plan and strategies for achieving this goal to succeed. Here are some tips on how:
- Create an ISO 9001 system with goals, objectives, policies, and procedures that guide your company on process improvement initiatives;
- Implement value chain analysis which includes evaluating the strengths of each link or step within the sequence from raw material acquisition through product delivery;
- Develop standardized work instructions, so employees know what is expected at every stage of production
- More supervision from supervisors to track the production process and monitor the performance of employees. This will help with adjustments or corrections if needed during this process.
- Rewarding more employees for their hard work when they exceed expectations, which is a great motivator, encourages other workers to do the same.
- Providing more training for employees to help them understand how lean management works, what a good job looks like, and what they are expected to put in place when it comes time for production. This will allow workers to improve their skills so that there is less room for errors or mistakes.
- Eliminate waste by analyzing process flow and eliminating bottlenecks for increased efficiency.
- Streamline work processes with kaizen to increase potential productivity in the workplace while reducing production costs at every step along the way. This could be achieved through implementing a standardized layout throughout your facility or optimizing inventory levels. Hence, there’s always enough product on hand when needed without having too much-unused stock sitting around waiting to enter into circulation again later down the line as necessary supplies are depleted from available resources like raw materials, human labor, and machinery/equipment maintenance downtime should be scheduled periodically beforehand rather than scrambling last minute because it would reduce energy expenditure which will translate that back onto savings.
Conclusion
While lean management is a complex subject, we’ve done our best to summarize the basics and provide you with all of the information you need to create an effective plan for your company. If you have any questions or would like more guidance as you go about this process, be sure to reach out! We’re happy to help. So sign up now and share on social media today so others can learn how they too can apply these principles at their workplace.