Disclaimer: We sometimes use affiliate links in our content. For more information, visit our Disclaimer Page.
In business, several different costing methods can be used. One of the most popular is absorption costing. Absorption costing is a full costing method that allows companies to track the total costs associated with producing and selling their products or services.
This guide will discuss absorption costing, how to use it, alternatives, and the benefits of doing so.
Let’s get started!
What is Absorption Costing? (Definition)

In business, the term “absorption costing” refers to a method of accounting for all costs associated with manufacturing a particular product. This includes direct and in-direct costs, such as direct materials, direct labor, rent, and insurance. The idea behind absorption costing is that all of these costs should be accounted for in the product’s final cost.
This method is often used in managerial accounting as it provides a more comprehensive picture of the true cost of manufacturing a product. While absorption costing may not be the most intuitive or straightforward method of accounting, it can provide valuable insights into the true cost of manufacturing a product. As such, it can be a helpful tool for decision-making.
Absorption costing vs. variable costing
The main difference between absorption costing and variable costing is how they treat fixed manufacturing overhead costs. In absorption costing, fixed manufacturing overhead costs are included in the product cost, while in variable costing, all fixed manufacturing overhead costs are treated as period costs. This means that in absorption costing, every product manufactured in a specific period has a portion of the fixed manufacturing overhead costs included in its product cost.
In contrast, variable costing only assigns variable manufacturing overhead costs to each product since all fixed manufacturing overhead costs are considered period costs. As a result, the product cost is higher in absorption costing than in variable costing. However, some argue that absorption costing gives a more accurate picture of the actual cost of a product since it includes all manufacturing costs. Others say that variable costing is more effective in decision-making since it isolates the impact of changes in volume on fixed and variable costs.
Ultimately, it is up to each business to decide which method is more appropriate for their needs.
Related: Cost Structure
How to calculate absorption costing? (3 Simple Steps)
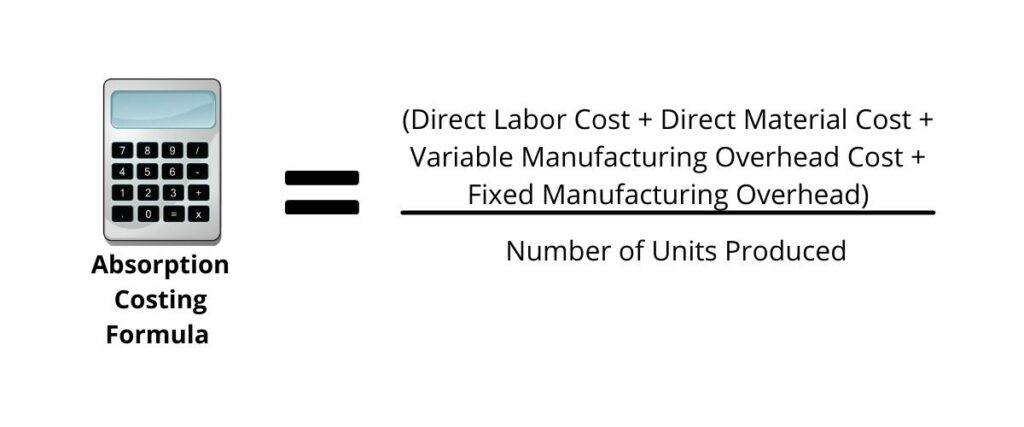
Here are some absorption costing calculations and assignment procedures:
1. Develop cost pools
Determine the expenses associated with the production of a product and then allocate them to different cost pools. Expenses are grouped into cost pools based on their purpose. For example, marketing, customer service, and research and development might be divided into separate cost pools. You’ll assign costs to the pool that best reflects your expenditures once you’ve spent money.
For example, if you spend $100 on advertising, you would assign that cost to the marketing cost pool. If you spend $50 on customer service, you will assign that to the customer service cost pool.
You can use any system of grouping expenses into cost pools that make sense for your business. However, it is important to be consistent in how you group costs to compare apples to apples accurately.
2. Determine the allocation base
To determine the cost of each activity, you will need to figure out the usage for each activity. This includes the labor or equipment usage hours throughout the manufacturing process.
For example, if you are manufacturing a product that takes two hours to produce and have one worker paid $10 per hour, the labor cost for that activity would be $20.
Once you have determined the usage for each activity, you can allocate the costs accordingly. This will help you better understand where your money is going and how to optimize your production process.
3. Calculate the absorption rate
Finally, determine the allocation rate, which tells you how much it costs to produce each item. You may calculate this by using the following equation:
Absorption cost per unit = (Direct Material Costs + Direct Labor Cost + Variable Manufacturing Overhead Costs + Fixed Manufacturing Overhead Costs) / Number of units produced
What are the Benefits of Absorption Costing?
There are several benefits of using absorption costing:
1. Tracking profits
Absorption costing gives a company a more accurate picture of profitability, especially if all of its products are not sold during the same period when they are manufactured. This is an important consideration if a company plans to ramp up production in anticipation of a seasonal sales increase.
2. Measuring inventory
Another benefit of the absorption costing method is that it provides a company with a more accurate measure of the value of its inventory. This can be important when deciding whether to sell or hold onto inventory. In addition, inventory carried on the balance sheet at its full cost (including both variable and fixed costs) gives stakeholders a better idea of the company’s overall financial health.
3. Accounting for all production costs
When determining product pricing, it is essential to consider all the costs associated with production. Absorption costing is a method that considers every cost, making it an invaluable tool for price setting. This information allows companies to ensure that their product’s price point covers expenses involved in production.
It also enables them to price their products more competitively within their market. However, to make sound pricing decisions, it is essential to understand all the costs involved in production. Absorption costing provides this vital information, making it a valuable tool for any company looking to stay competitive in today’s marketplace.
4. Appropriate for smaller firms
Fixed costs do not fluctuate with changes in production levels, making them more difficult for smaller firms to manage. However, these costs must still be accounted for when determining the price of a product. Absorption costing allows small businesses to consider all of their production costs, ensuring that they are pricing their products appropriately.
5. Simplicity
While other costing methods may be more complex, absorption costing is relatively straightforward. This makes it an appealing option for companies looking for a simple way to track and manage production costs. Additionally, cost pools can help further simplify the process by grouping similar expenses.
6. Changes in demands are anticipated
Companies that use absorption costing can more easily adapt to changes in demand. This is because all the costs associated with production are already factored into the product’s price. As a result, companies using this method do not need to make any significant changes to their pricing when demand fluctuates.
What are some Disadvantages of absorption costing?
Absorption costing has several benefits and also drawbacks. Some of the disadvantages of absorption costing are as follows:
1. Overproduction to cut costs
As any business owner knows, one of the critical ways to increase profitability is to lower your costs. One way to do this is by overproducing your product. By producing more units than you need, you can reduce the cost per unit by spreading out the fixed overhead costs.
This can be a great way to boost your bottom line, but it only works if you can manage to sell all of the units you produce. If you have unsold units, the fixed overhead costs will eventually be transferred to your expense reports, which will eat your profits. So while overproduction can be a great way to cut costs, you must ensure you can sell everything you produce.
2. Insufficient data
Incomplete data can lead to inaccurate conclusions. This is especially true when fixed overhead is included in the data used to determine a product’s cost through absorption costing. Fixed overhead is a necessary component of production, but it can inflate the actual cost of manufacturing.
As a result, the data used for analysis may be insufficient to provide a comprehensive picture. Incomplete data can also result from other factors, such as methodology or sampling error. Whatever the cause, it is crucial to be aware of the potential for inaccuracy and take steps to avoid it. Otherwise, you may end up with an incomplete picture that doesn’t give you the whole story.
3. Over-assigning overhead costs
Even overhead expenditures that can’t be directly traced to the product are charged against each unit. This can lead to inflated unit costs and, ultimately, higher prices. This could make your products less competitive in the marketplace and result in lower sales.
Despite these disadvantages, Absorption Costing remains a popular method for managing production costs. When used correctly, it can be a valuable tool for any business looking to stay competitive in today’s marketplace.
An Example of Absorption Costing
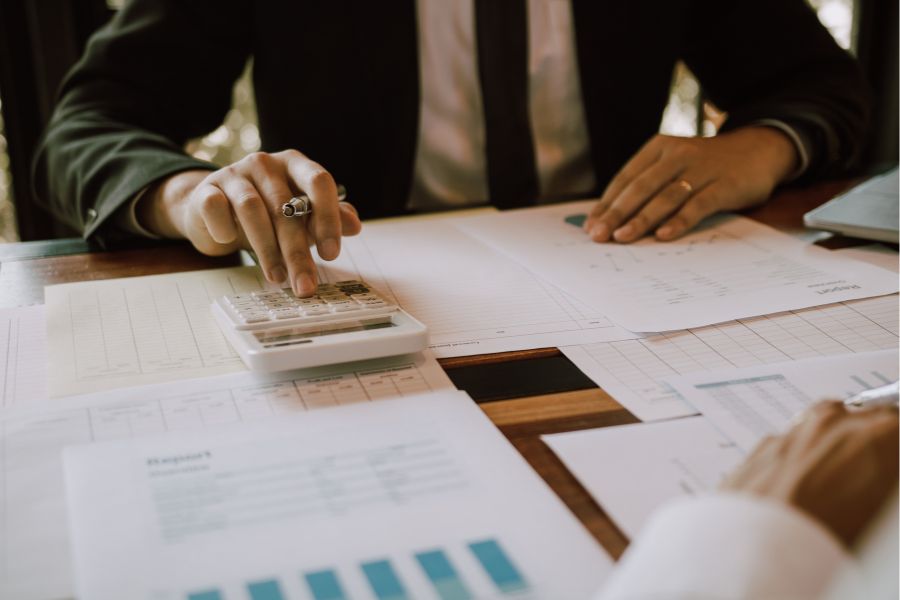
In the accounting period, a firm produced 60,000 units. With 10,000 in stock, it marketed 50,000 units. Each item was sold for $100 per unit. Manufacturing overhead was $10 plus $5 in variable administrative expenses per item. The following expenses were paid: $300,000 in manufacturing overhead and $200,000 in fixed administration costs. Absorption cost per unit was calculated using the following equation:
(Direct Material Costs + Direct Labor Costs + Variable Manufacturing Overhead Costs + Fixed Manufacturing Overhead Costs) / number of units produced.
($25+$20+$10+$300,000 / $600,000 = $60 per unit product cost.) In absorptive costing, the inventory in the company’s warehouse (10,000 units) is valued at $600,000.
Alternatives to Absorption Costing
There are a few alternatives to absorption costing that businesses can use if they find the limitations of absorption costing too restrictive. These include variable costing, contribution margin analysis, and direct costing.
Variable costing is a form of cost accounting in which only variable costs are included in calculating cost per unit. This means that fixed costs are not considered, which can be helpful for businesses that experience changes in production volume.
Contribution margin analysis is a technique used to calculate the amount of contribution margin per unit. This allows businesses to see how much revenue they need to generate from each product to cover their fixed costs.
Direct costing is another type of cost accounting that only includes direct materials and direct labor costs in the cost per unit calculation. This method can be helpful for companies that do not have fixed overhead expenses or other indirect costs that need to be considered when calculating their profit margins on each product manufactured.
Final Thoughts
Absorption costing is a method of allocating fixed and variable costs to products or services. The main advantage of absorption costing is that it can more easily adapt to changes in demand. However, there are some disadvantages to using this method, such as the potential for overproduction and insufficient data.
Despite these drawbacks, Absorption Costing is still a popular way to measure production costs. When used correctly, it may be an important tool for any business seeking to stay competitive in today’s market.
An example of Absorption Costing is provided to illustrate how this method works in practice. Ultimately, it is up to each business owner to decide if Absorption Costing is the proper method for their company.
Thanks for reading! We hope this guide was helpful.
FAQ
What is the absorption costing formula?
The absorption costing formula is used to calculate the full cost of a product, including all manufacturing costs and overhead expenses (materials + labor + variable production overhead + fixed production overhead) ÷ (number of completed units).
What are the types of absorption costing?
There are three main types of absorption costing: full, variable, and mixed. Full absorption costing includes all manufacturing costs in the product cost, while variable and mixed only have some manufacturing costs.
What is absorption costing vs marginal costing?
Absorption costing assigns all manufacturing costs and overhead expenses to products or services, while marginal costing only assigns direct materials and direct labor costs. Marginal costing is also known as variable costing.
What is absorption costing and variable costing?
Absorption costing is a method of calculation that assigns all manufacturing costs and overhead expenses to products or services. Variable costing is a similar method of calculation that only assigns direct materials and direct labor costs.
How do you calculate under absorption and absorption costing?
To calculate under absorption, take the total cost of goods sold and subtract the variable costs. To calculate absorption costing, take the total cost of goods sold and add the fixed costs.
What are overhead absorption costs?
Overhead absorption costs are all the expenses incurred in manufacturing a product, including fixed and variable costs. These costs are then divided by the number of units produced to calculate the overhead absorption cost per unit.